Cultivated meat media and growth factor trends
GFI and TurtleTree Scientific explore key insights from a 2020 cultivated meat industry survey that dives deep into current practices within the space, the direction and pace of progress, ways to close inefficiency gaps, and how to best meet manufacturer requirements.
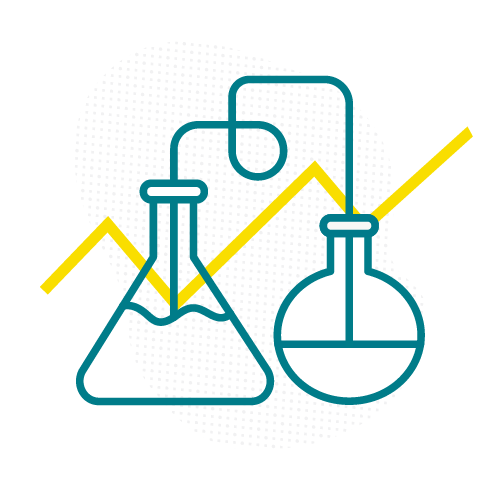
Forecasting demand to feed a growing world
The cultivated meat industry aims to feed a growing global population and to reduce the negative impacts associated with conventional animal meat production by manufacturing real meat from cultivated animal cells. While the industry has rapidly expanded over the past six years, there remains a lack of publicly available information needed for forecasting and future planning. Specifically, more information is needed to develop rigorous demand forecasts for commercialized products and process inputs and to inform anticipated production cost reductions over time.
Mapping industry trends with real-world industry data
Cell culture media compose the majority of current cultivated meat production costs. The majority of these costs are incurred by the recombinant proteins and growth factors added to media to assist cell growth and differentiation and to substitute the function of animal serum. To better understand how cell culture media and growth factors are being used and developed by the cultivated meat industry, a questionnaire was sent in late 2020 to cultivated meat manufacturers and suppliers of growth factors and media interested in supplying the industry. Based on responses to this survey from 19 cultivated meat manufacturers and 21 suppliers of culture media components or formulations, we have distilled a snapshot of this emerging industry’s current progress and needs, with an eye toward future demands and cost reduction prospects.
Rapid progress has been achieved, but further improvements will be needed
The data collectively shows that cultivated meat manufacturers have made significant progress in reducing costs and developing medium formulations for various cell types and cultivated species. Many suppliers have begun to make adjustments to meet the unique requirements of the cultivated meat industry. Still, some inefficiencies between supply and demand were observed, such as pricing and availability of species-specific and food-grade versions of growth factors. The analysis presented here includes extensive insights into the industry’s current practices, the direction and pace of progress, ways to close inefficiency gaps, and how to best meet the requirements of cultivated meat manufacturers.
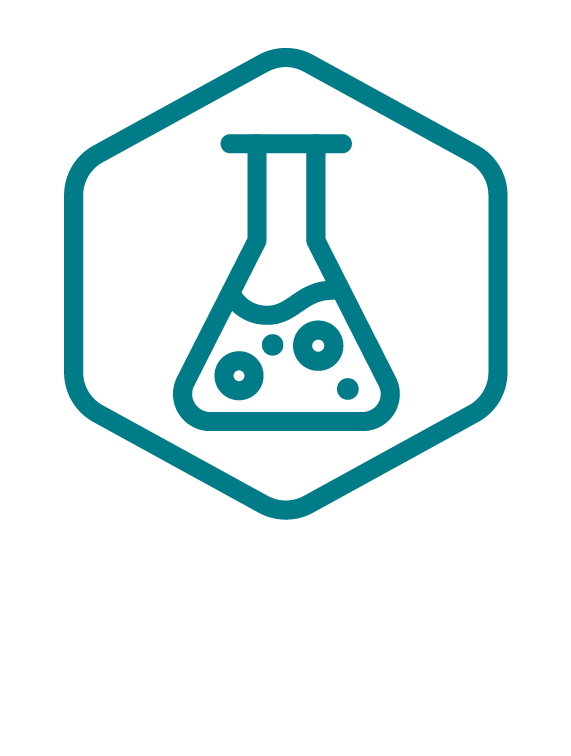
Key research ideas based on survey results:
- Assessing hydrolysate-based cell culture media to understand the raw material sources that perform best for cultivated meat applications and provide insights on how to limit variability and improve reproducibility.
- Analyzing the performance of feed-grade ingredients in cell culture medium.
- Comparative analyses between species-specific versions of growth factors.
- The development of medium recycling technologies.
- Adaptation of cell lines for lower growth factor requirements.
- Discovering plant-based protein homologues for animal growth factors.
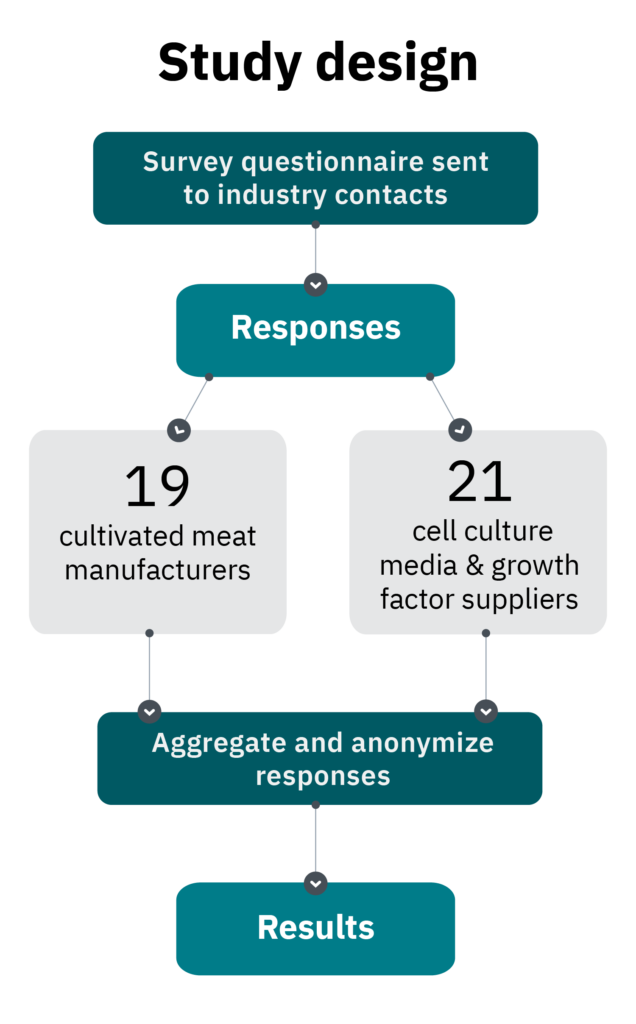
Surveying the cultivated meat industry
In December 2020, a questionnaire was sent to all known cultivated meat and milk manufacturers and all known cell culture media suppliers or suppliers of recombinant proteins and growth factors (hereafter growth factors) interested in supplying the cultivated meat industry. A total of 19 cultivated meat or milk manufacturers and 21 cell culture media or growth factors suppliers that aim to service the cultivated meat industry responded.1
Suppliers ranged from well-established companies that service multiple industries to early-stage startups that are still developing their first products. At the time of surveying, manufacturers had been in operation for an average of 2.5 years. We believe this survey represents the cultivated meat industry, with some skew in the data possible in manufacturer responses, which may be biased toward companies in earlier stages of maturity. Additional information about the survey respondents can be found in Manufacturer and supplier information below.
1 To encourage the highest possible response rates, respondents were not required to answer all questions; some answered the majority of questions while others answered only a partial set of questions. Reported percentages are rounded to the nearest whole number. To incentivize participation, companies that contributed data received early access to the comprehensive aggregate findings, with the understanding that this condensed summary would be made publicly available after an embargo period.
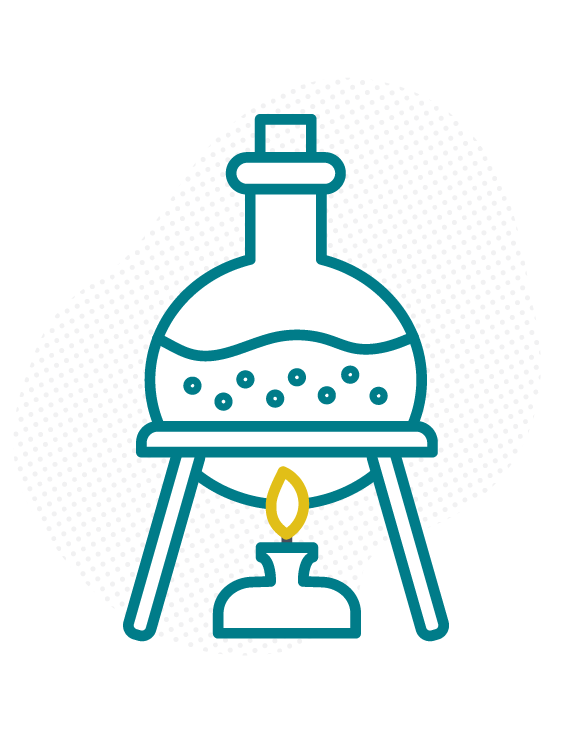
Manufacturer and supplier information
Manufacturers work with a broad range of cell lines and produce a broad range of cell types. Suppliers who aim to service the cultivated meat industry leverage their expertise in supplying other industries.
Manufacturer information
In the next 12 months, manufacturers across the industry anticipated producing an upper sum of approximately 1400 kg of cultivated meat (Fig. 1, n = 17). When asked when they anticipate moving beyond pilot scale, 16% of respondents indicated in the next one to two years, 63% in three to four years, and 21% in four to six years (n = 19).
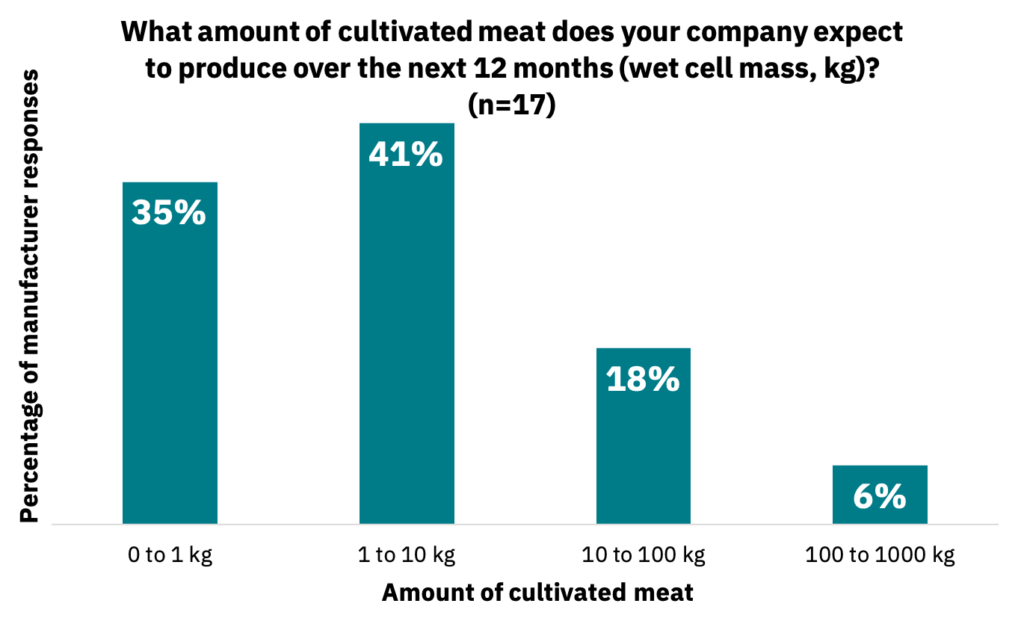
Most manufacturers are still in the research and development phase.
These data show that the manufacturers in this survey are likely heavily focused on R&D rather than commercial production. The establishment of pilot-scale production facilities is expected to coincide with small-scale commercial releases over the next few years. Once manufacturers move into actual commercial facilities beyond pilot scale, their production volumes will dramatically increase, which will enable more product availability at lower production costs (Vergeer, R., Sinke, P., Odegard, I. 2021).
Cell lines and types
Manufacturers work with a variety of cell lines and cell types, including cell lines from multiple species. For instance, 61% work with three to four species, and 34% work with just one to two (n = 18). Manufacturers indicated that they work with between one to 10 cell lines, with a range of one to 10 cell types. 89% of manufacturers indicated they plan to expand the number of cell lines they work with over the next 12 months (n = 19). The types of cells used (n = 18) and produced (n = 19) by manufacturers are indicated below (Fig. 2-3).
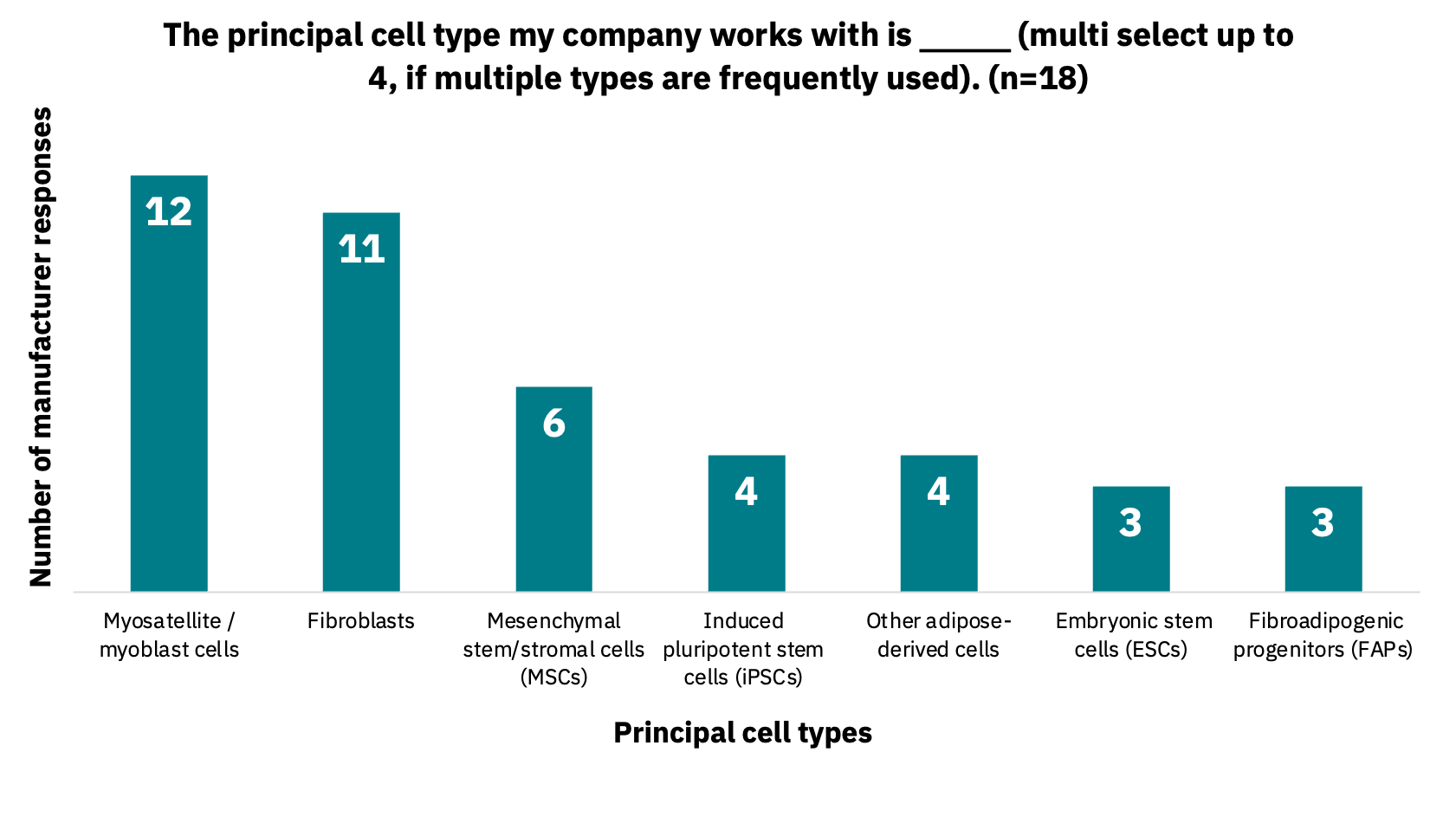
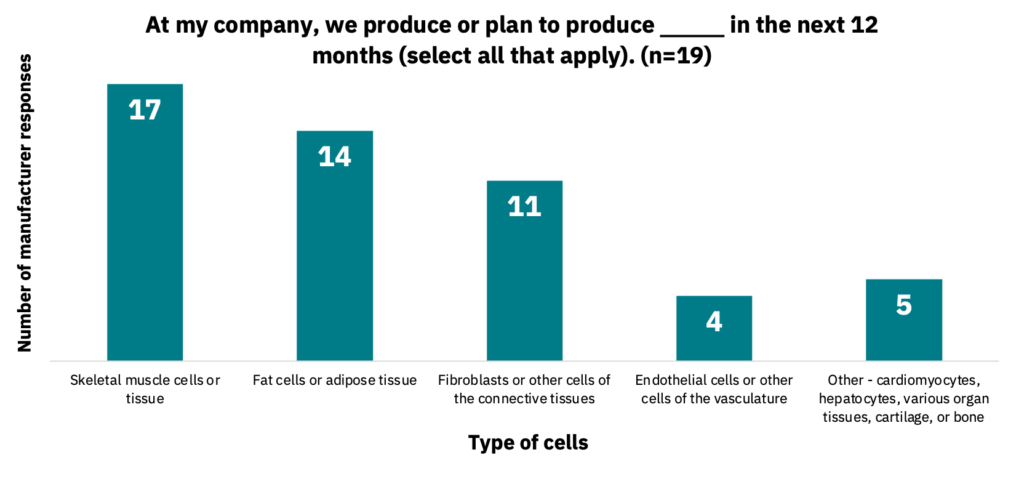
Manufacturers use a diverse set of cell lines and create many cell types.
There appears to be no industry consensus on cell type selection by manufacturers, with multiple starting cell types often used in parallel. Manufacturers are primarily creating cells that comprise meat (skeletal muscle, fat, and connective tissues) but in some cases are also producing cells for vasculature or other tissues, including cartilage, bone, and cardiac muscle. The diversity of starting cells, cells being produced, and species has important implications for suppliers in creating cell culture media formulations or key ingredients specific to manufacturers’ requirements.
Supplier information
Suppliers responded that they generally have a good sense of the cultivated meat industry’s requirements when it comes to growth factors (72%) and cell culture media (62%) (Fig. 4-5, n = 21).
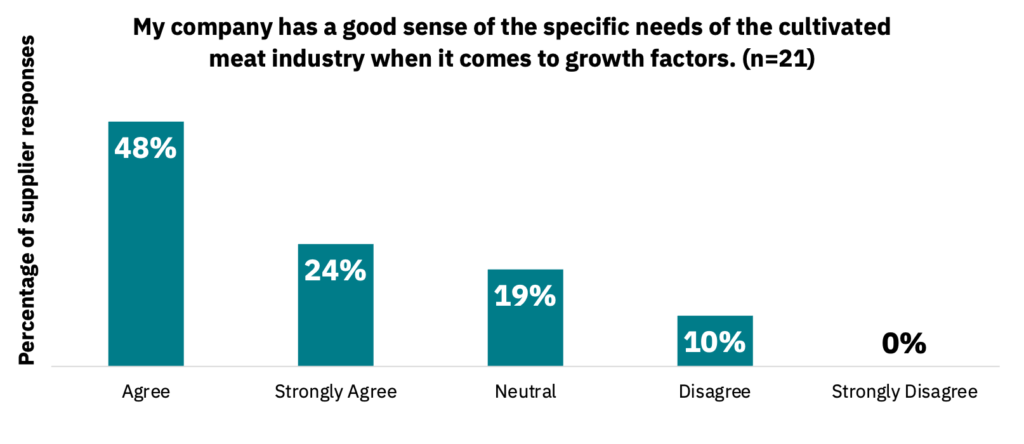
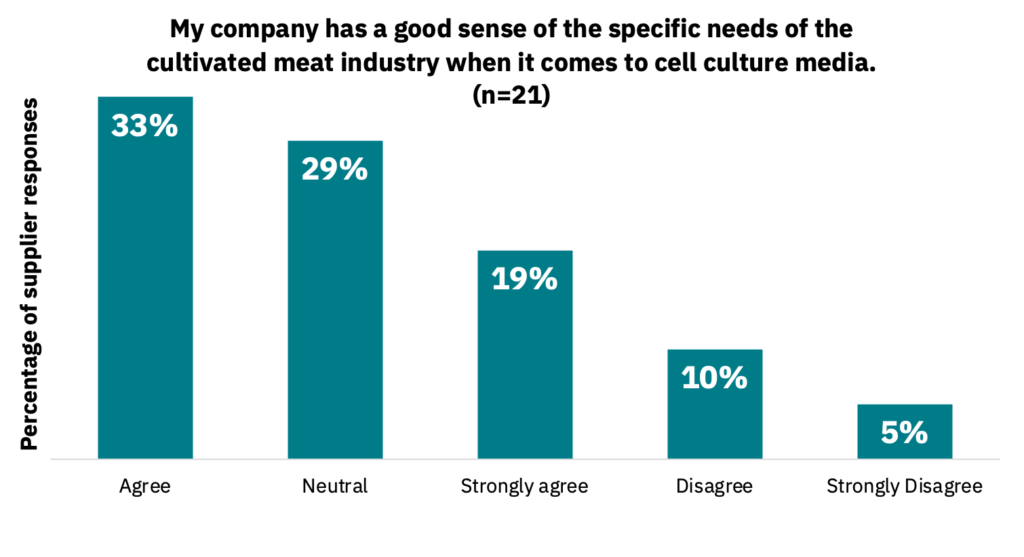
Suppliers manufacture a variety of different product categories (Fig. 6, n = 20). They also sell products to multiple different industries (Fig. 7, n = 16), with other cited industries including diagnostics, vaccines, probiotics, and cosmetics.
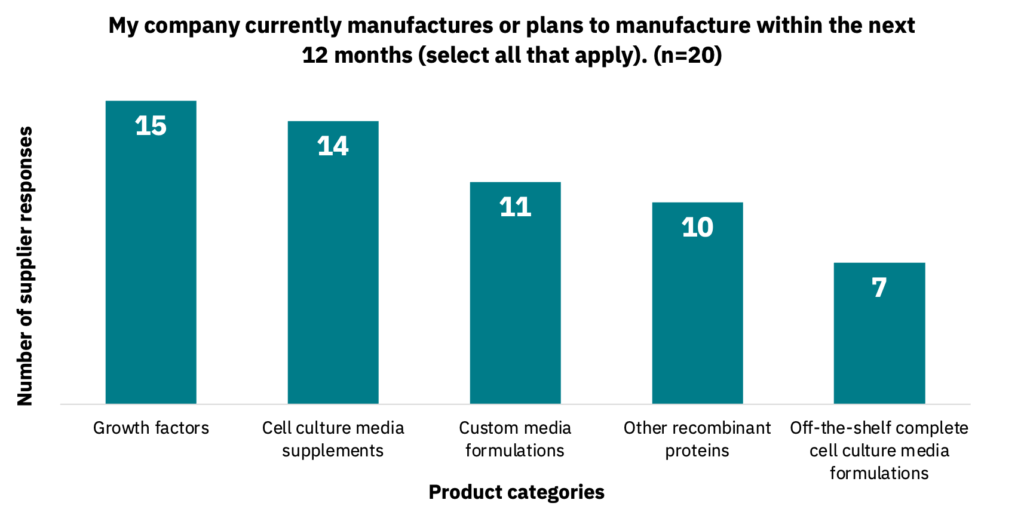
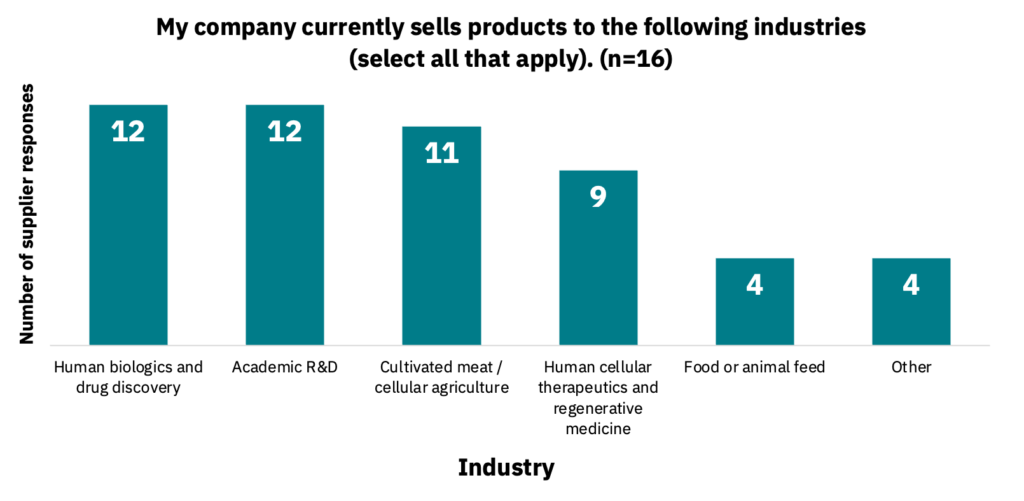
Media types produced by suppliers
Cell culture media suppliers produce products for a variety of cell types (Fig. 8, n = 11), but often optimized for cell lines commonly used in other industries but with limited relevance to cultivated meat, such as monkey (Vero), insect (SP2), or canine (MDCK) cells.
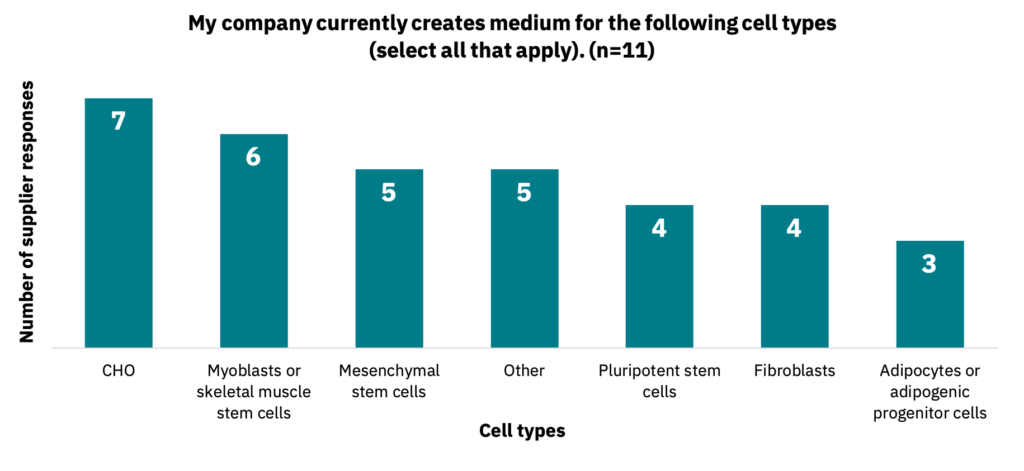
Supplier participation in the cultivated meat industry
The majority of suppliers perceive the cultivated meat industry as a customer right now, with others viewing the industry as a potential customer in the future (Fig. 9, n = 21).
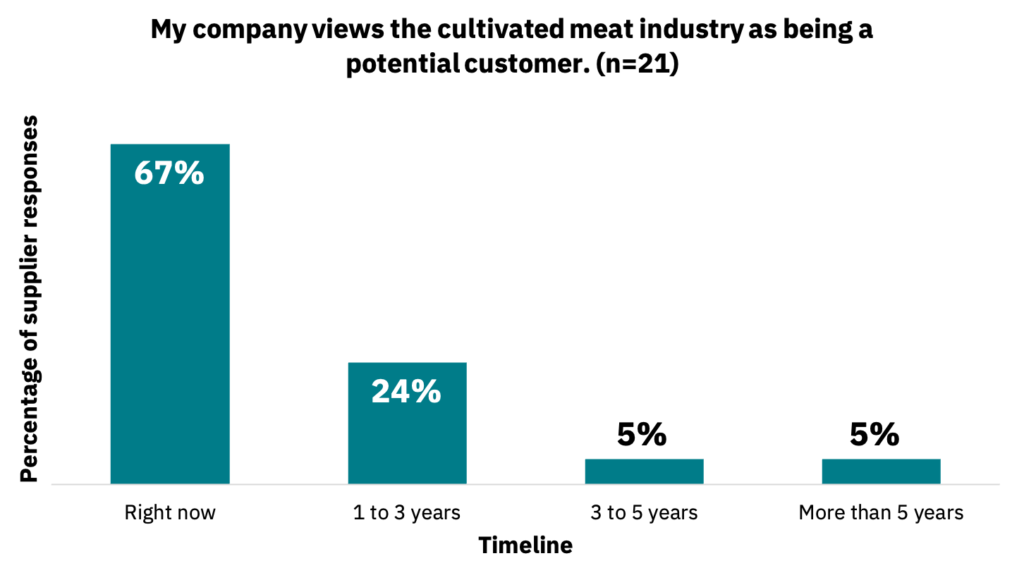
Some suppliers view the cultivated meat industry as making up most of their business within the next five years, with others anticipating less involvement (Fig. 10, n = 21).
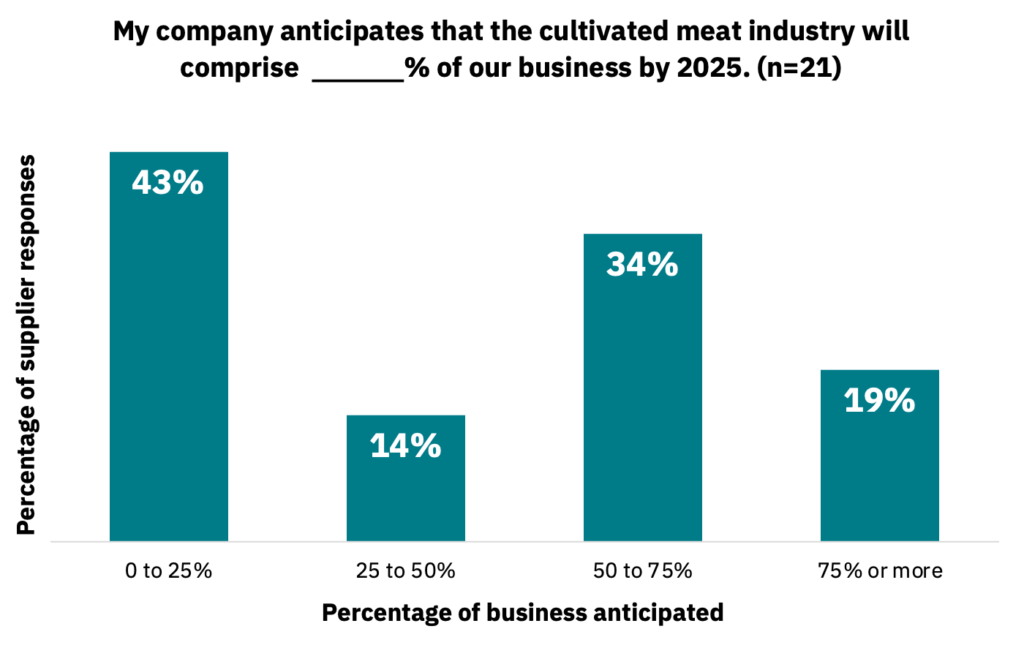
Suppliers service other industries in addition to cultivated meat.
These data show that suppliers interested in cultivated meat are typically already supplying other industries and can leverage their expertise to create products for the cultivated meat industry. Suppliers will likely not be limited to one specific industry unless by choice. These additional business options could be advantageous for early-stage startups that aim to grow alongside the nascent cultivated meat industry.
Interestingly, other business options are not limited to suppliers. At least two cultivated meat manufacturers (Avant Meats and Integriculture) have launched product lines for the skincare industry.
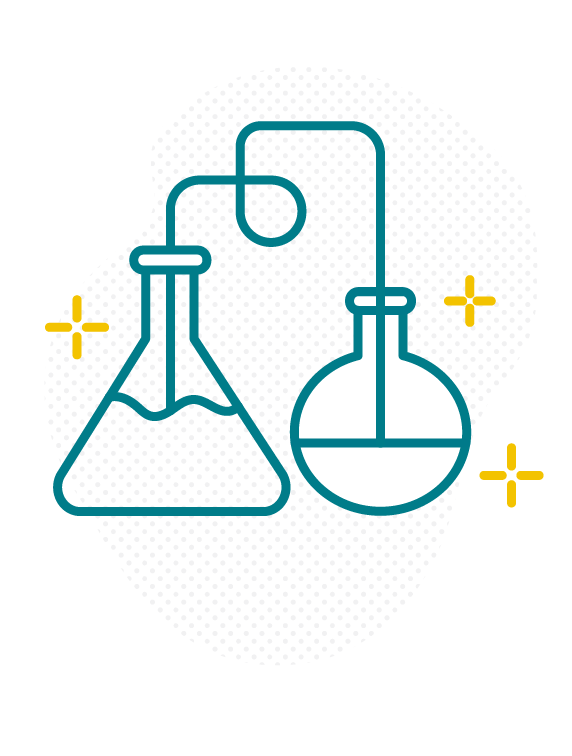
Growth factor production and characteristics
Suppliers and manufacturers use a variety of production platforms to produce growth factors. The industry is moving toward food-grade production of species-specific growth factors and exploring ways to optimize their production.
Growth factor production platforms
Suppliers are currently using various production platforms to produce growth factors, including bacteria, fungi, and plants (Fig. 11, n = 14). 21% of suppliers also mentioned using cell-free systems for production.
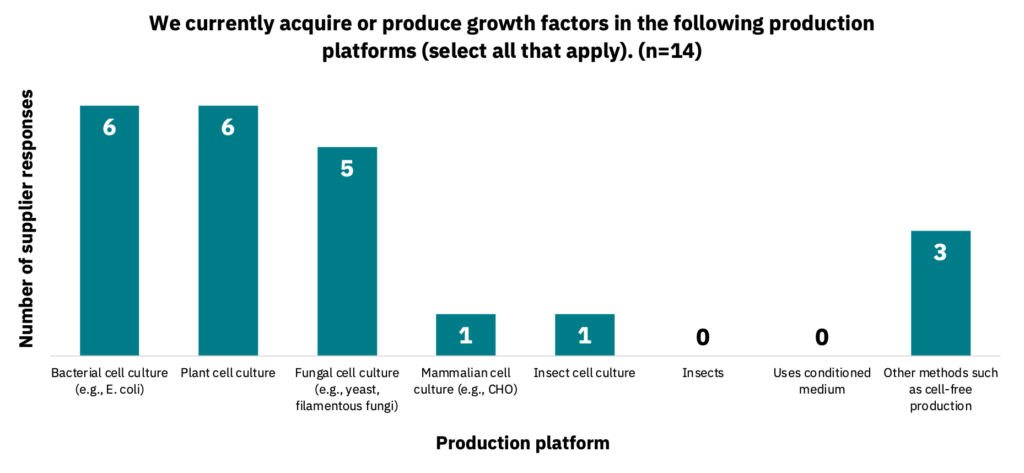
For manufacturers, a similar trend was observed for production platforms used when acquiring or producing growth factors (Fig. 12, n = 15). 79% of suppliers (n = 14) and 67% of manufacturers (n = 6) stated they are actively seeking ways to produce growth factors in non-mammalian systems.
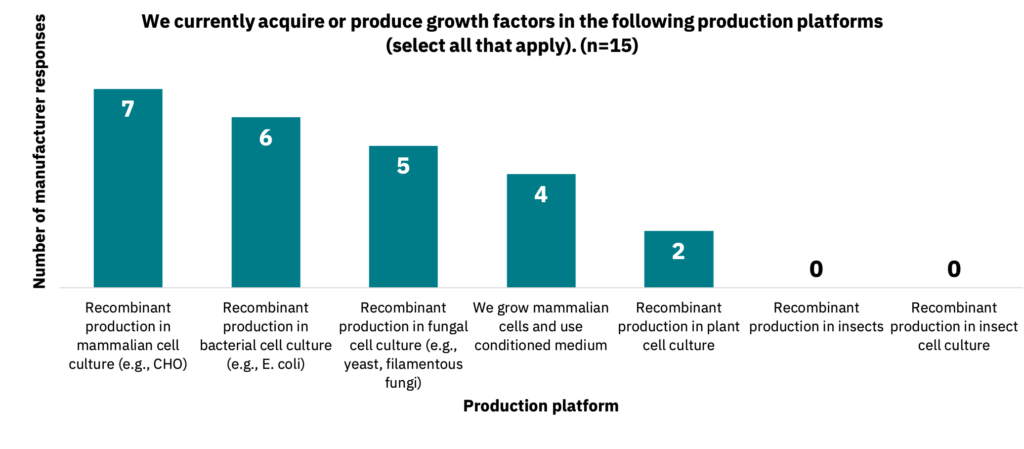
A variety of production platforms are used to produce growth factors.
Both manufacturers and suppliers use many different production platforms to produce growth factors. Recent announcements suggest this list is expanding to include insects as well. An assessment of pros and cons for each production platform may be helpful in understanding which platform may be most suitable in terms of costs, environmental impacts, or other relevant parameters for the specific types of growth factors used in the cultivated meat industry.
In-house production
Interestingly, 40% of manufacturers produce growth factors in-house, with an additional 35% of manufacturers interested in producing growth factors in-house (n = 16). Manufacturers indicated various percentages for the amount of growth factors produced in-house versus being outsourced to a third party (Fig. 13, n = 15).
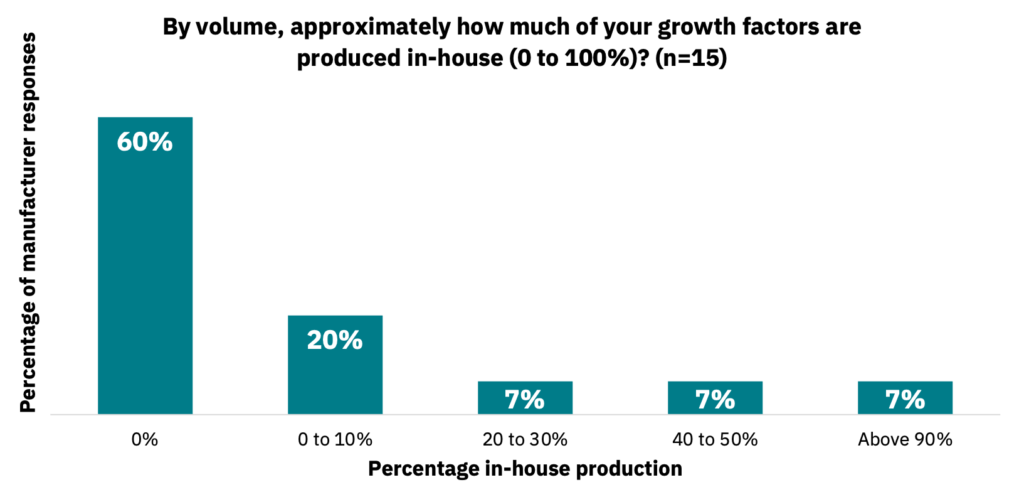
Of those producing growth factors in-house, the primary reasons are that external supplier costs are too high or that their requirements are unique, among other factors (Fig. 14, n = 15). Despite this, 60% of manufacturers stated they plan to buy primarily from a supplier within the next 12 months, with 40% preferring in-house production (n = 15).
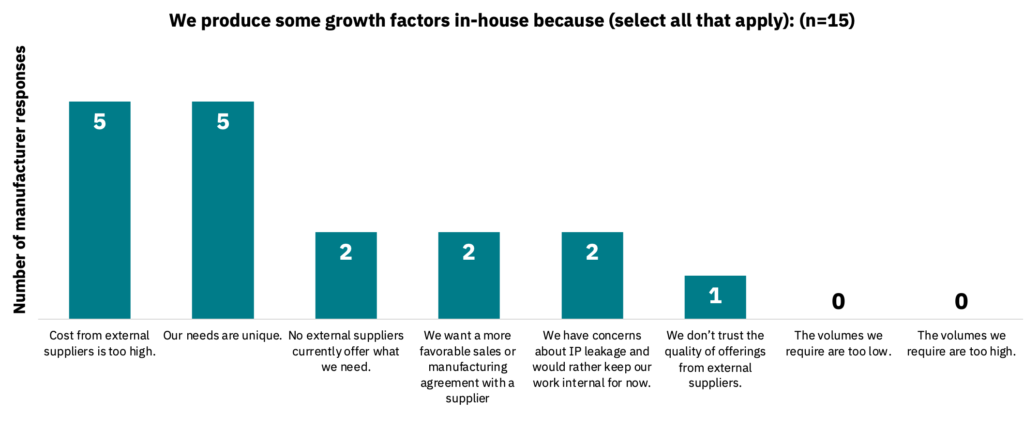
In-house growth factor production by manufacturers can form new intellectual property.
67% of manufacturers stated that they view the in-house production of growth factors as part of their intellectual property portfolio, which gives them a competitive advantage (n = 15). 27% of manufacturers stated they had plans to file patents related to growth factor production, with 27% being unsure and 46% with no plans (n = 15).
Suppliers can make adjustments to better service the cultivated meat industry.
These data suggest that there is a current opportunity in the marketplace for growth factors. Manufacturers appear to be leaning toward in-house production of growth factors, citing high costs and unique requirements that make suppliers’ current off-the-shelf products unattractive. While some manufacturers may be doing this strategically to create intellectual property, the majority plan to purchase from a supplier within the next 12 months. Suppliers should use the data in this survey to better understand and adjust to meet the growth factor requirements of the cultivated meat industry.
Food-grade growth factors
Currently, approximately 33% of manufacturers acquire or produce their growth factors at food-grade purification standards (n = 15)2. Of the manufacturers that do not currently use food-grade growth factors, 90% stated they plan to in the next 12 months (n = 10). Notably, 100% of manufacturers stated that they did not observe reduced bioactivity, cell toxicity, or contamination issues when using food-grade growth factors (n = 5).
While many suppliers produce their growth factors at pharmaceutical or research-grade today, many anticipate switching to food-grade in the next 12 months (Fig. 15, n = 13 and n = 14). 57% of suppliers stated they have food-grade production pipelines in place (n = 14). Of these suppliers, 14% observed reduced bioactivity, cell toxicity, or contamination issues for their food-grade growth factors (n = 7).
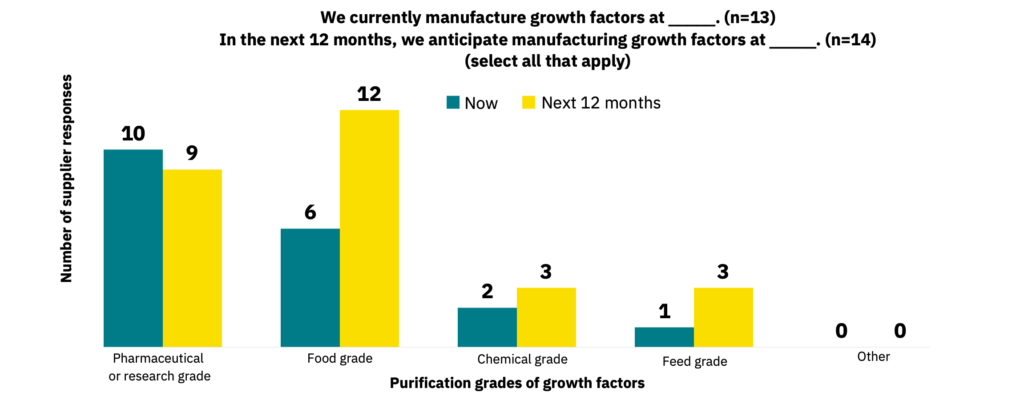
Food-grade growth factors are in high demand.
Growth factors used in food production do not need to be produced to the same rigorous purification standards as in the pharmaceutical industry, enabling lower production costs. Cultivated meat manufacturers plan to capitalize on this by using growth factors produced at food-grade standards. Suppliers are playing catch-up and must follow through on establishing food-grade growth factor offerings to remain attractive to the cultivated meat industry.
2 For more on purification standards in food and pharma, see https://www.usp.org/reference-standards and https://www.foodchemicalscodex.org/.
Species-specific growth factors
Seven manufacturers indicated that they are currently using species-specific growth factors for some cells, with additional manufacturers claiming they would be interested in purchasing them from suppliers or using species-specific growth factors in the future. Only two manufacturers indicated that they do not use species-specific growth factors at all (Fig. 16, n = 16).
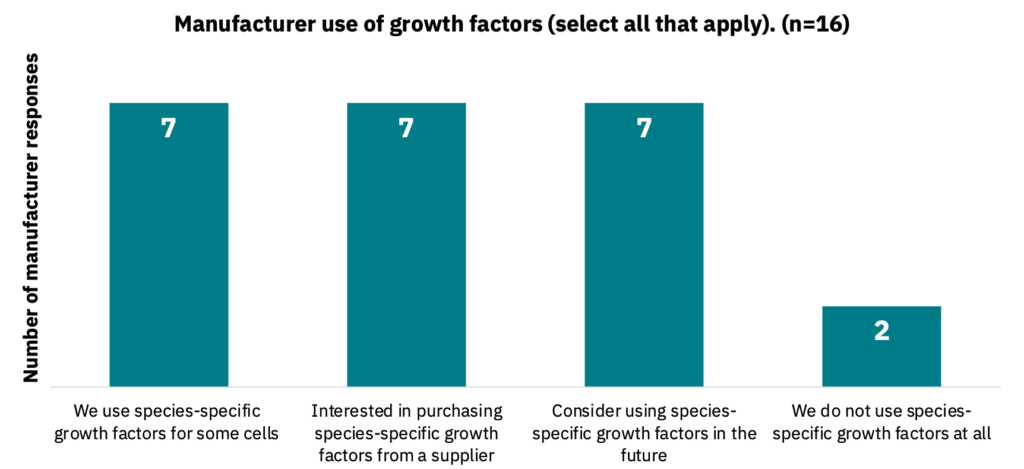
Manufacturers prefer to use species-specific versions of growth factors.
Given the variety of species being used in the cultivated meat industry, demand for species-specific growth factors ultimately increases the number of growth factors that need to be produced. This may force suppliers to focus on only a subset of species and growth factor types based on potential market size. Gaps in unique or smaller market growth factor production by suppliers for specific species or types may present opportunities for smaller supplier startups to fill. Alternatively, this niche demand may be filled through in-house production by manufacturers.
Growth factor alternatives and recycling
Because growth factors are the most expensive input in the cell culture medium, discovering plant-based substances that replace their function or recycling them could lower the overall cost burden of growth factors.
33% of suppliers stated they are currently exploring plant-based substances as replacements for growth factors, 21% may plan to in the future, and 46% have no plans to do so (Fig. 17, n = 12).
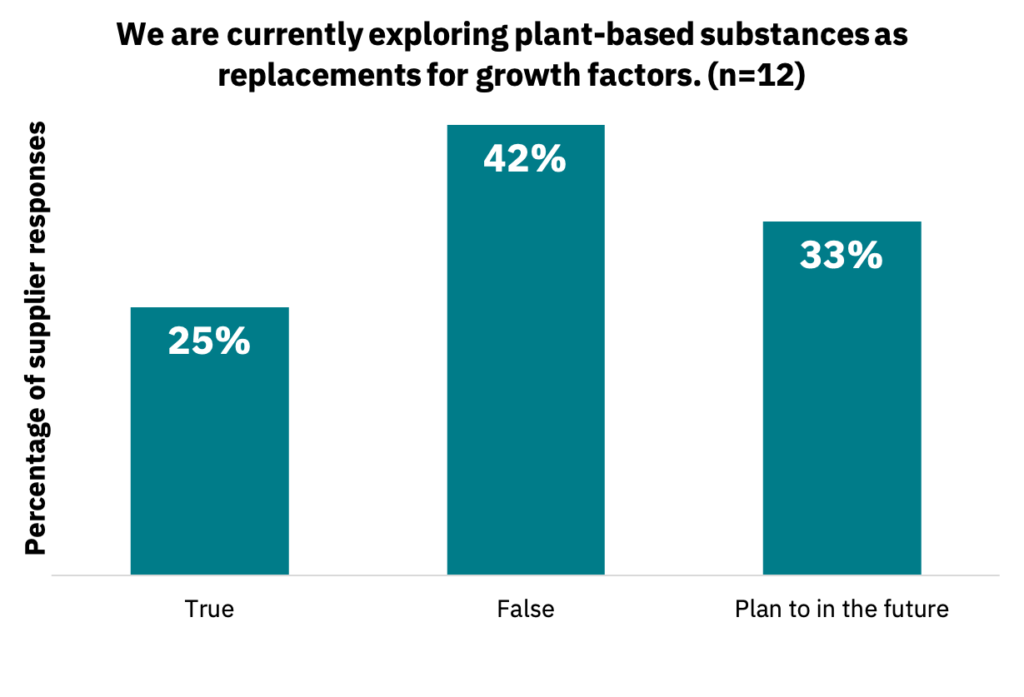
Manufacturers would use plant-based replacements or recycling equipment if they were available.
82% of manufacturers are not using plant-based substances as replacements (n = 17), but 72% of manufacturers responded that they would prefer to, provided those replacements compete on performance and cost (n = 18).
Only one manufacturer (7%) indicated that they recycle growth factors (n = 14), whereas 41% of manufacturers would be interested in purchasing recycling equipment if it were available (n = 17). Similarly, only 12% of manufacturers indicated that they monitor growth factors or growth factor levels (n = 16), but 63% are interested in purchasing growth factor monitoring equipment or tools (n =16).
Engineered growth factors
Successful engineering or modification of growth factors could reduce cell culture media costs by requiring fewer numbers of growth factors or a smaller amount of growth factors.
Engineered growth factors are in demand.
54% of suppliers perform genetic engineering or modification of growth factors in-house. 31% plan to in the future, and 15% have no plans (n = 13). 47% of suppliers stated that cultivated meat manufacturers had approached them to create custom-engineered growth factors (n = 15).
33% of manufacturers indicated that they do not use engineered or recombinant growth factors due to concerns about regulation or consumer acceptance (n = 15). 20% of manufacturers indicated that they have plans to commercialize or license growth factors that they’ve engineered in-house, with another 53% indicating that they were unsure (Fig. 18, n = 15).
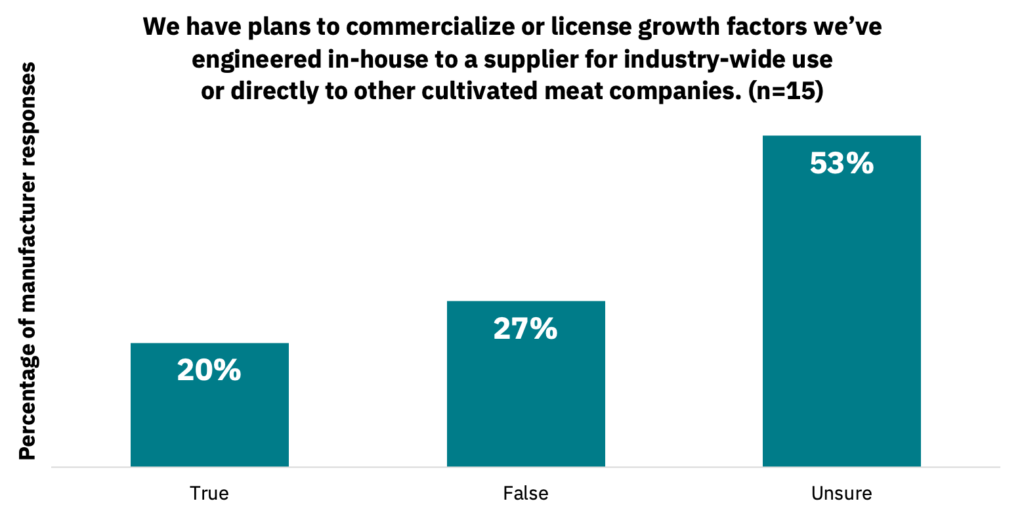
There are many ways to improve growth factors.
Suppliers (n=14) and manufacturers (n=13) cite several characteristics that are of interest for growth factor engineering (Fig. 19). Other characteristics cited for improvement include cost, acceptability to consumers, non-GMO-certifiability, and low residue levels in final products.
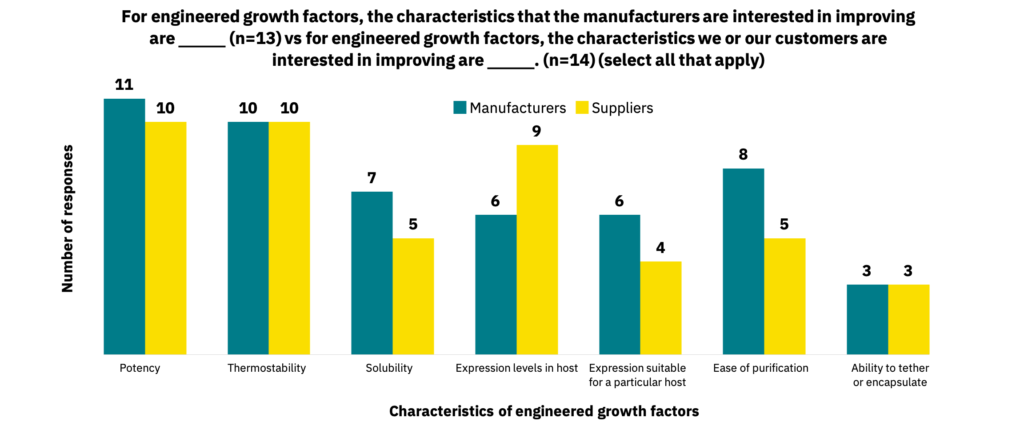
Adaptation approaches are promising routes to lowering growth factor use.
12% of manufacturers indicated that they have adapted or engineered their cell lines for reduced growth factor requirements (n = 16), resulting in a 50- to 80-percent reduction in use (n = 2).
Other approaches to modify growth factors are being trialed in the industry.
13% of manufacturers indicated that in the next 12 months they intend to modify their animal cell lines to produce growth factors that are not normally expressed within those cells (n = 16).
93% of manufacturers stated that they do not use any slow-release systems to reduce the total amount of growth factors used (n = 15).
Manufacturers anticipate primarily using growth factors that are soluble in the media, but other use-cases were also cited (Fig. 20, n = 17).
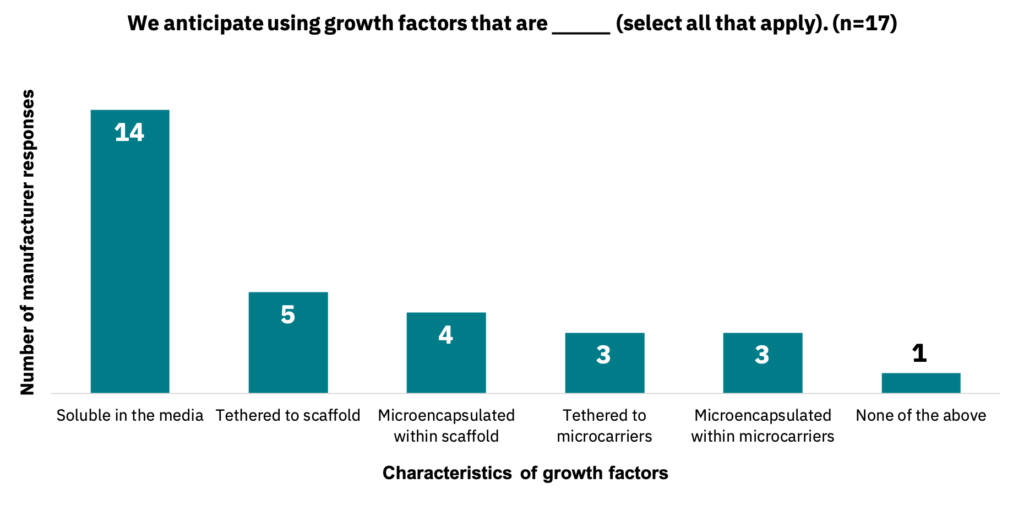
Growth factor summary
Manufacturers are exploring many ways to optimize the performance or cost of the growth factors they use. In particular, engineering of growth factors is being pursued, although there is some concern about the regulation or consumer acceptance of these methods. The data show that there are many opportunities for suppliers to meet the needs of cultivated meat manufacturers for growth factor optimization.
Adaptation of cell lines, recycling equipment or tools, and plant-based substitutes are key whitespace opportunities for lowering the cost burden of growth factors.
Although few manufacturers have tried, adaptation or engineering of cell lines for reduced growth factor requirements has resulted in 50- to 80% reductions, making these methods cost-effective for other manufacturers to pursue. Furthermore, many manufacturers would be interested in growth factor recycling or monitoring equipment or tools, making this an attractive whitespace opportunity for existing suppliers, new entrants, and academic research endeavors.
Many manufacturers are currently exploring or plan to explore plant-based substitutes for growth factors. Achieving this could dramatically reduce costs across the cultivated meat industry. One example of success is Future Meat, who has stated that an albumin homolog in chickpea can replace recombinant albumin protein, resulting in a 60% cost reduction of their media formulations. Albumin, often used at higher concentrations than other growth factors, accounted for 80% of recombinant protein costs in a recent techno-economic analysis (Vergeer, R., Sinke, P., Odegard, I. 2021).
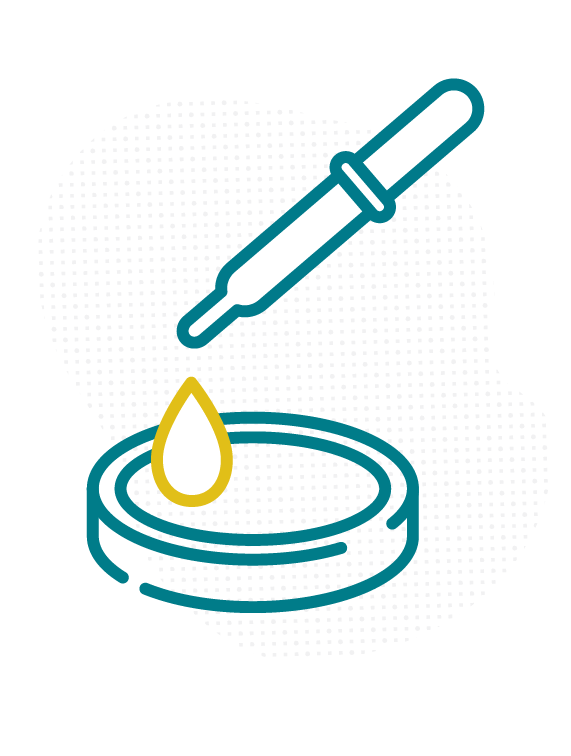
Cell culture media
Suppliers and manufacturers are shifting toward food-grade media components and creating optimized formulations unique to cultivated meat production’s cell lines and species.
Cumulative media use
Across R&D and production, manufacturers indicated that they anticipate using the following amounts of media in the next 12 months (Fig. 21, n = 18).
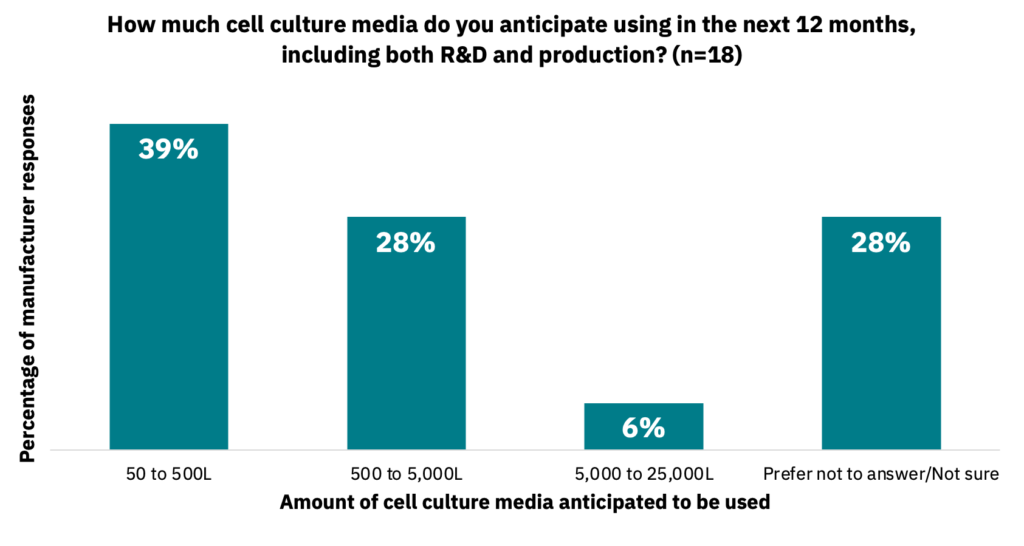
Food-grade basal media components
Pharmaceutical or research-grade basal medium components such as amino acids, glucose, and vitamins make up the majority of ingredients that manufacturers are currently working with (n = 16) and what suppliers are sourcing (n = 9). Still, food-grade and feed-grade basal medium components are anticipated to become more heavily used within the next 12 months (Fig. 22-23).
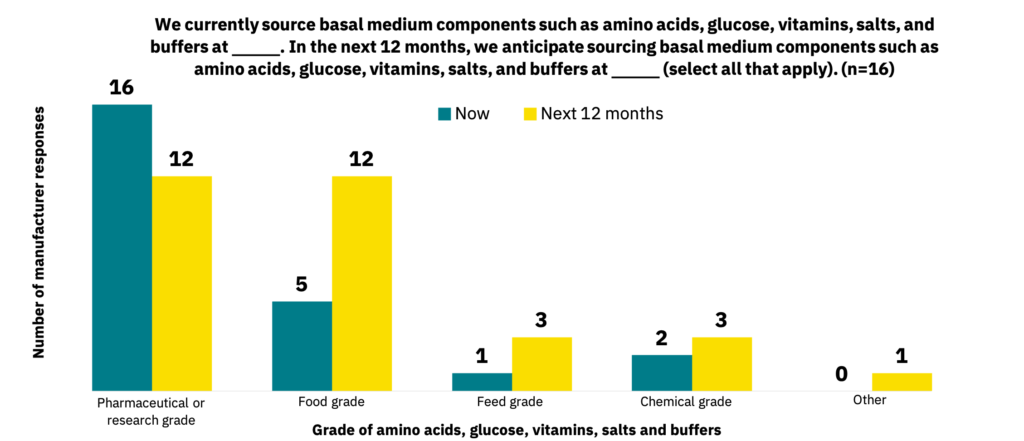
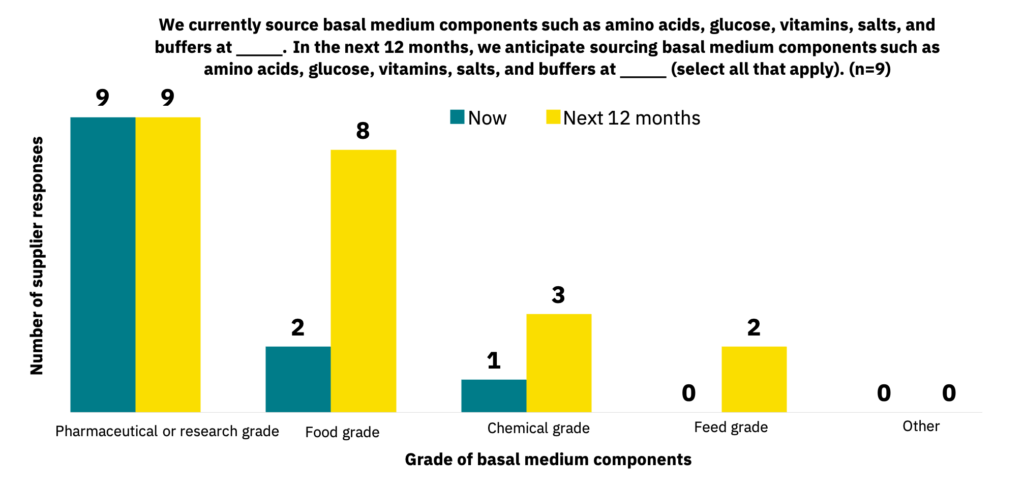
A food-grade supply chain is still in development.
As with growth factors, manufacturers and suppliers currently source basal medium components predominantly at pharmaceutical-grade standards but anticipate a significant switch to food-grade or feed-grade components over the next 12 months, which can further reduce costs. Given that manufacturers are not yet using significant quantities of cell culture media, this timeline seems appropriate for paralleling the industry’s growth. In general, suppliers aiming to service the cultivated meat industry should produce or source their medium components at food-grade or feed-grade standards, depending on the ingredient and use case. As documented below, manufacturers have cited some challenges with using protein hydrolysates, and crude feed-grade ingredients could pose similar challenges for performance or reproducibility.
Identifying the primary raw material sources and assessing their performance are important research areas.
Open-access research analyzing the performance of feed-grade ingredients in cell culture medium would be beneficial for assessing their utility in the cultivated meat industry. Additionally, a greater understanding of cellular metabolism is needed to inform the ratios of basal medium ingredients within media formulations to optimize media use efficiency and feeding regimens.
Sourcing, quality, and sterilization
57% of manufacturers stated that they source their amino acids from protein hydrolysates for some or all formulations (n = 14). 43% of manufacturers stated they use combinations or blends of protein hydrolysates to fit their amino acid requirements (n = 14). 38% of manufacturers purchase amino acids produced via fermentation for some or all of their medium formulations (n = 13). 36% of manufacturers said that the amino acids they use are optimized according to the metabolic profiles of their cells (n = 14).
A more diverse set of protein hydrolysates may be used in the future.
The protein hydrolysates cited by manufacturers included soy and cottonseed, while suppliers noted they supply hydrolysates from soy, wheat, pea, cottonseed, rice, and yeast. Some manufacturers noted that lot-to-lot variation and the chemically undefined nature of protein hydrolysates pose challenges. Manufacturers also noted that they wish there were more suppliers of food-grade growth factors, lipids, and microalgae-derived components.
62% of manufacturers purchase individual vitamins produced by fermentation or chemical synthesis for some or all of their medium formulations (n = 13). 67% of manufacturers have their vitamin requirements met for some or all of their medium formulations by those contained within hydrolysates that they use (n = 12).
Quality and consistency of basal media components need improvement.
31% of manufacturers noted quality issues or inconsistencies with basal medium components, with another 31% being unsure (n = 16). 31% of manufacturers consider the country of origin as being important for sourcing basal medium components (n = 16).
Manufacturers noted membrane sterilization as the most common mode of medium sterilization (Fig. 24, n = 13).
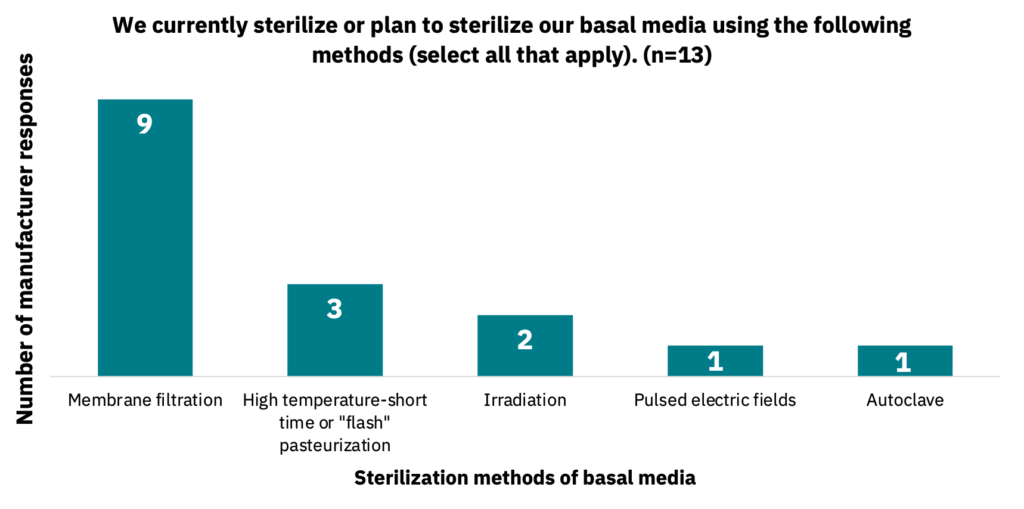
Raw material sourcing has important socioeconomic consequences.
The sourcing of basal medium components, which will make up the principal inputs for cultivated meat, has important implications for the future supply chain of cultivated meat and how farmers can participate actively in the industry. While manufacturers currently cite the use of soy and cottonseed hydrolysates, it’s possible that additional crops or other sources such as microalgae could be used for supplying the industry with amino acids. Some manufacturers have observed inconsistencies in their basal medium ingredients and have noted some difficulty in working with chemically undefined amino acids in the form of hydrolysates. Open-access research using hydrolysate-based cell culture media could assist in understanding the raw material sources that perform best for cultivated meat applications and provide insights on how to limit variability and improve reproducibility.
Media formulations
13% of manufacturers plan to commercialize or license their medium formulations to a supplier for industry-wide use or directly to other cultivated meat companies (n = 16).
Media formulations may be unique and undefined.
31% of manufacturers noted that their formulations have unique ingredients that are not included in standard commercial formulations (n =16). 44% of manufacturers indicated that all of their medium formulations are chemically defined (n = 18).
44% of manufacturers use or plan to use metabolic flux analyses, and 75% of manufacturers use or plan to use spent medium analyses to assist in their medium formulation efforts (n = 16).
Manufacturers prepare complete media on-site and source from third-party suppliers.
59% of manufacturers noted that some or all of their media are prepped on-site from dry powders (n = 17). 76% of manufacturers said that some or all of their media are shipped in liquid form after being prepped by a third-party supplier (n = 17).
Custom media formulations
47% of manufacturers indicated using a third party to outsource custom medium requirements (n = 17). Manufacturers cited several different barriers when working with third parties for custom medium formulations (Fig. 25, n = 15). Manufacturers also noted that they would like third-party suppliers to source and blend raw materials (including hydrolysates), use entirely animal-free ingredients, and help to reduce overall medium costs.
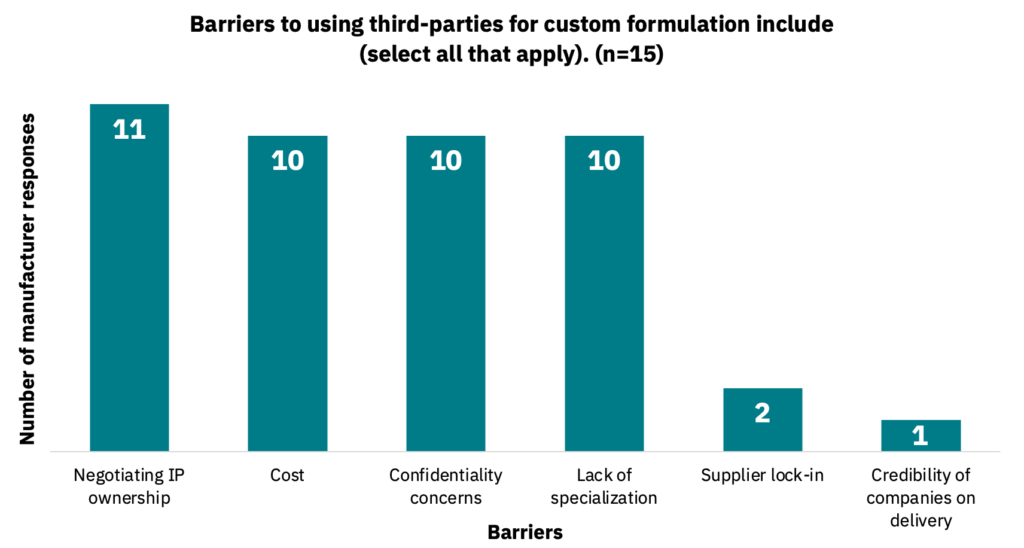
Not all medium formulations are customized.
39% of manufacturers noted that they do not use custom medium formulations for their proliferation media, while 33% do not for their differentiation media (Fig. 26-27, n = 18).

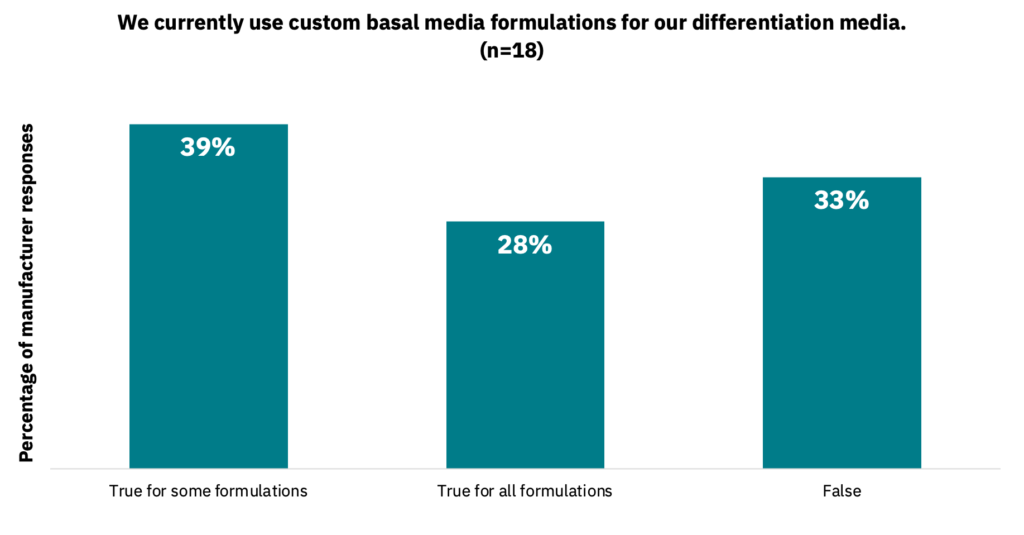
Of the manufacturers who do use custom formulations, 55% indicated that they use species-specific formulations (n = 11) and 70% use cell type-specific formulations (n = 10).
57% of suppliers stated they create or supply custom medium formulations (n = 14). Of these suppliers, 50% stated that the IP is owned by the customer when pursuing custom formulation agreements (n = 6).
Suppliers tend to only engage in custom formulation efforts if manufacturers request at least 1000 L of media. 69% of suppliers stated they are interested in serving as co-manufacturers of custom medium formulations developed elsewhere (n = 13).
71% of suppliers indicated that they could create custom serum-free medium formulations (n = 14), and 54% indicated that they could create medium formulations where all ingredients are at least secondary animal origin-free (n = 13), meeting many of the demands of manufacturers cited above.
Suppliers and manufacturers could work more efficiently to create custom medium solutions.
Significant progress has been made in producing serum-free medium formulations suitable for growing the range of species and cell types used by cultivated meat manufacturers. Surprisingly, not all of these formulations are custom, which could mean that off-the-shelf formulations designed for other cells are suitable for cultivated meat or that some manufacturers have not yet settled on a fully customized formulation. Manufacturers appear split on whether to use third parties for medium formulation discovery or to do the work in-house, citing concerns around IP, cost, and confidentiality. Suppliers could adjust their business models or practices to better accommodate the needs of cultivated meat manufacturers.
Cultivated meat suppliers and manufacturers can help ensure academic research does not fall behind.
Although not included in the survey, there is a growing number of cultivated meat researchers in academia. Generally, these individual labs will not have the resources to create custom medium formulations and often use serum-containing media as the default. Cultivated meat manufacturers could make it significantly easier for more academic scientists to begin research programs in cultivated meat, reduce costs, and reduce the reliance on serum for media by licensing the serum-free formulations that they’ve optimized and having standard suppliers produce it. Commercializing custom medium formulations can also reduce repetitive work within the industry and enhance the reproducibility and translatability of academic studies into the commercial realm. Increasing the availability of open-access, off-the-shelf medium formulations for cultivated meat would benefit the entire industry.
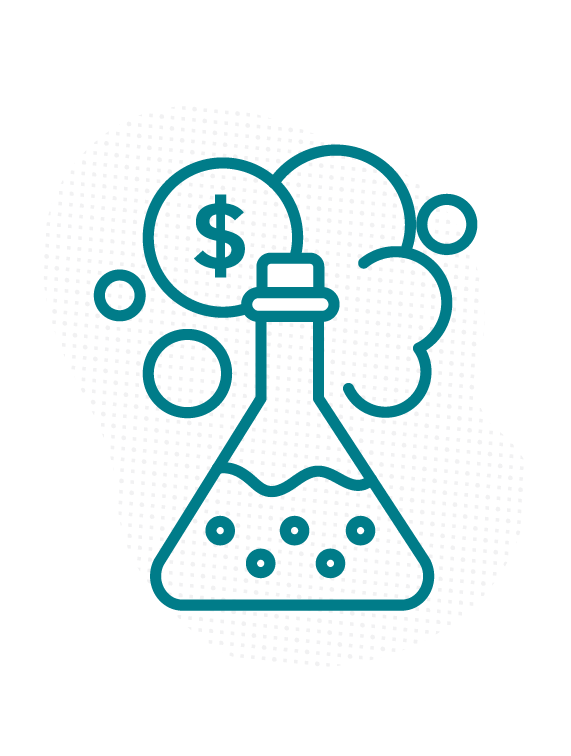
Cell culture media and growth factor costs
Significant progress has been made on reducing the most costly inputs—media and growth factors—throughout the industry.
Media costs
Manufacturers indicated that medium generally accounts for most of their variable operating costs (Fig. 28, n = 8).
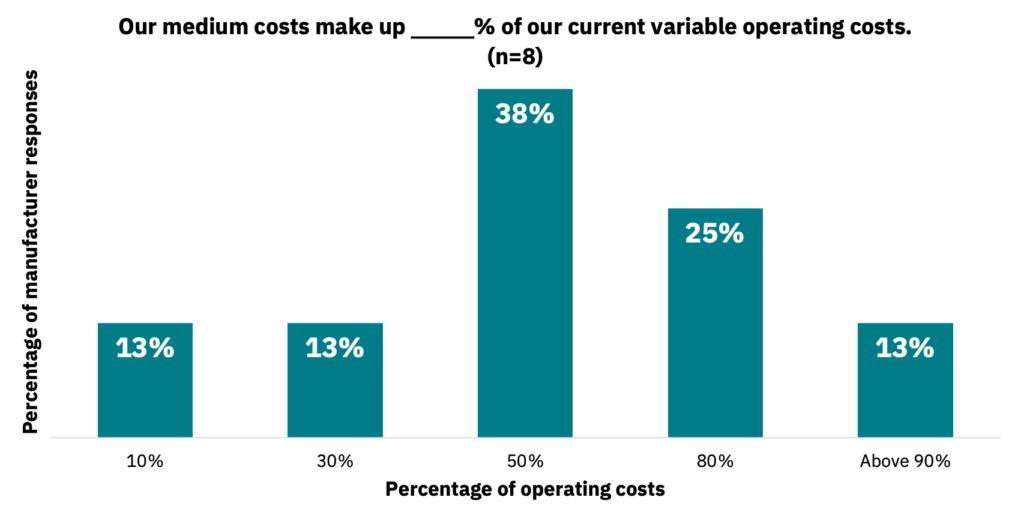
Manufacturers are achieving massive media cost reductions.
33% of manufacturers stated that they anticipate acquiring or producing their complete medium ingredients at a cost below $1.00 USD per liter in the next 12 months (Fig. 29, n = 15). Suppliers also anticipate that they will be able to significantly decrease medium production costs over the next five years. However, suppliers noted that this will be dependent on the growth factor requirements of the cells, which may lead to variable cost estimates (Fig. 30, n = 11).
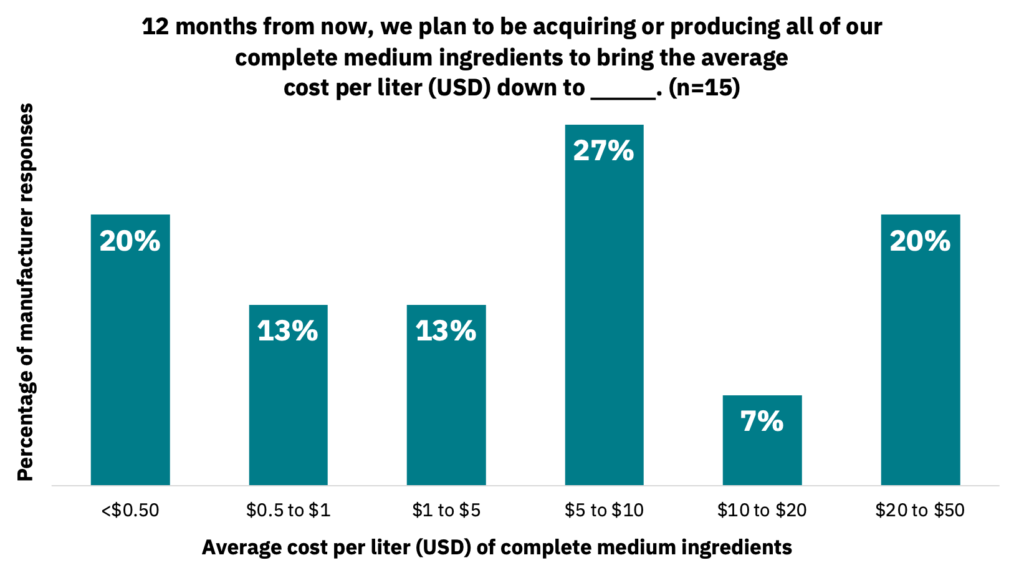
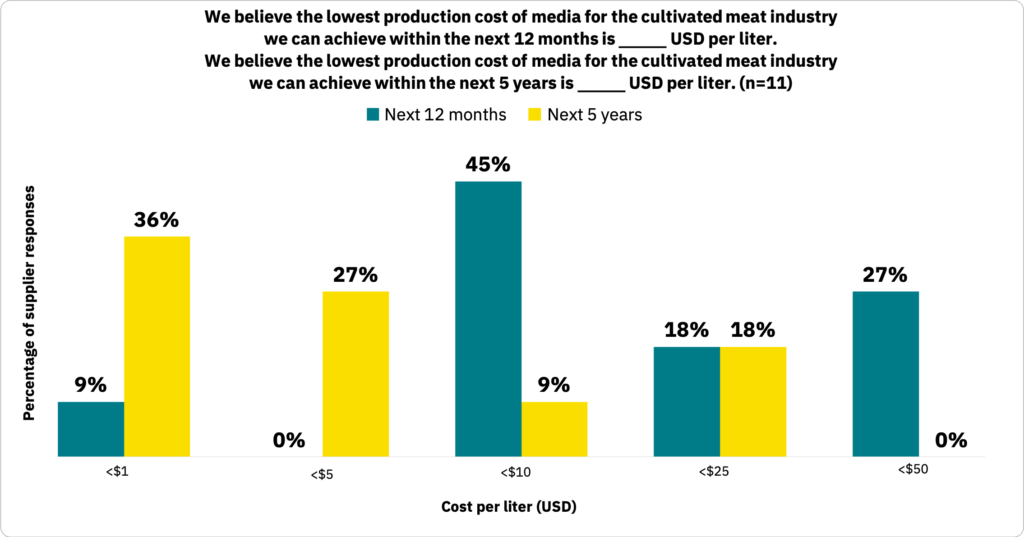
Supply-side pricing for media is still a work in progress.
Suppliers estimated that the lowest selling price of cell culture medium to maintain a viable business would be between $0.60 to $10 per liter (n = 11). Suppliers noted various barriers to lowering costs across their cell culture medium products (Fig. 31, n = 10).
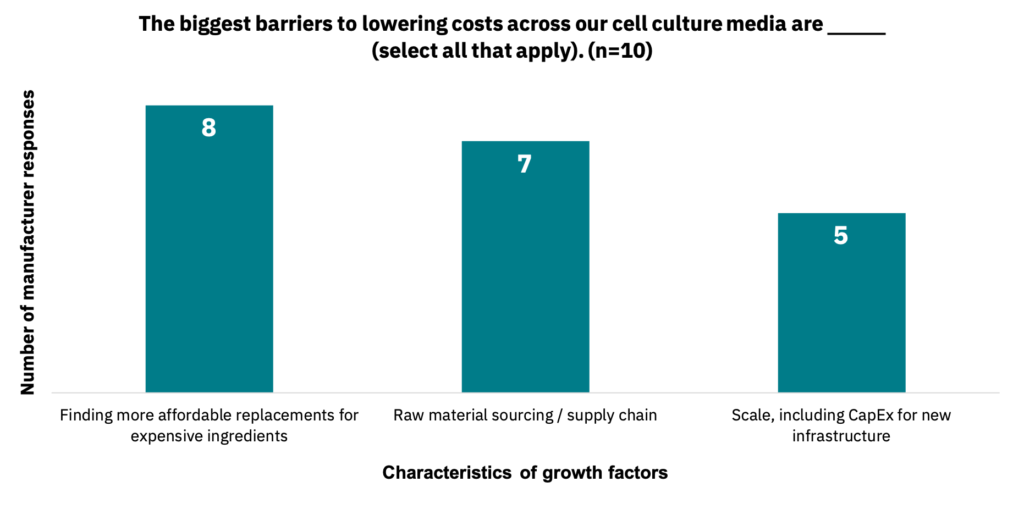
Industry progress points to media cost reduction being a smaller hurdle than originally anticipated.
Consistent with other reports, the cell culture medium was cited as a cost driver for manufacturers. Previous estimates suggested that cell culture medium costs could be reduced by 99% or more from current, off-the-shelf pricing for media containing pharmaceutical-grade components, hypothetically reaching costs as low as $0.24 per liter (Specht 2018). Because most off-the-shelf commercial media formulations for stem cell culture cost more than $100/L, cost reduction estimates less than $1/L represent at least a 99-percent cost reduction.
The survey data confirmed that these cost reduction estimates are already within striking distance for some manufacturers. Some expect to achieve < $1/L production costs for their medium within the next 12 months. Recent reports from Mosa Meat have also hinted at media cost reductions of 99%. The majority of suppliers also indicated that over the next five years, medium production costs per liter could drop below $5 and, in some cases, below $1. Suppliers also indicated that the sales prices of media could also fall below $1/L, with upscaling and sourcing affordable raw materials and key ingredients being important determinants for how low prices can reach.3 Collectively, these data support previous assumptions that cell culture medium production costs can be dramatically reduced in just a few years without requiring giant technological leaps.
3 The vast majority of media on a volumetric basis is water, and the true cost contribution of media for cultivated meat production will be a function of how efficiently the raw materials within the medium are metabolized into biomass. The more efficient the cell’s metabolism, the fewer liters of media will be needed for production. Refer to Table 16 from (Sinke, P., Vergeer, R., Odegard, I. 2021).
Growth factor costs
Most manufacturers indicated that growth factors make up 60 to 80% of their current medium costs, with one respondent indicating just 30% (n = 8).
The cultivated meat industry uses a shared set of growth factors.
Manufacturers were asked to list the top five to 10 growth factors they use based on total volume (mass) and cost. Responses produced a largely overlapping list of growth factors, displayed as a non-ranked list in Table 1.
Growth factor volume (mass) | Growth factor cost |
---|---|
Insulin | Insulin |
IGF1 | IGF1 |
FGF2 | FGF2 |
EGF | EGF |
LIF | LIF |
NRG1 | NRG1 |
TGFb1 |
Additionally, recombinant albumin is also likely a candidate for both categories based on data inventory from a recent techno-economic assessment (Vergeer, R., Sinke, P., Odegard, I. 2021).
Growth factor costs are expected to fall precipitously in the short term.
Suppliers indicated that the current production costs for growth factors range from $4 to $400,000 USD per gram (n = 4). Suppliers indicated that within the next five years, producing their most efficient growth factors would likely fall within a cost range of $1 to $100 per gram (n = 6). Suppliers noted various barriers to reducing growth factor manufacturing costs, with yield being the largest (Fig. 32, n = 14). Other barriers included the demand for higher scale operation and balancing high bioactivity with low production costs.
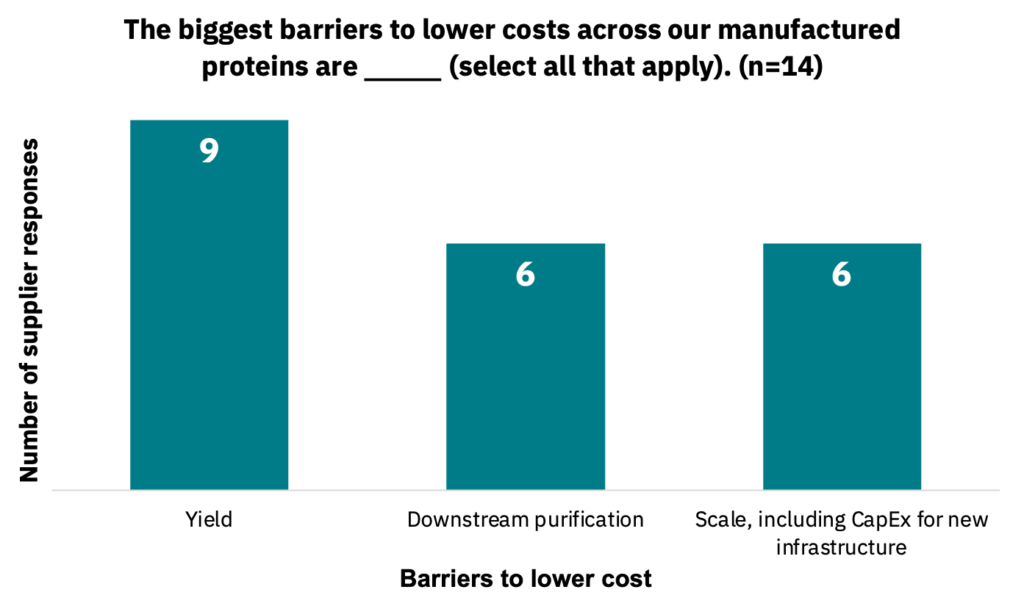
The current profit margin on growth factors for suppliers ranged from 30 to 90%, and suppliers estimated that margins needed to maintain a viable business were between 30% to 60% (n = 5).
With limited data available, manufacturers noted that their estimated costs of production for growth factors were between $50 to $2000 USD per gram when producing them in-house (n = 2).
Existing technologies can reduce growth factor costs to a nominal amount.
Survey data also corroborated other reports identifying growth factors as the primary cost driver of cell culture media (Vergeer, R., Sinke, P., Odegard, I. 2021). Suppliers cited wide ranges of current production costs for growth factors, spanning five orders of magnitude. However, suppliers also indicated that costs are expected to fall between $1 and $100 per gram within the next five years, reinforcing the notion that scaling up production of food-grade growth factors is sufficient to massively reduce growth factor production costs. If growth factor production costs within this range are achieved, the cell culture medium would no longer be expected to be the primary cost driver for cultivated meat manufacturers (Vergeer, R., Sinke, P., Odegard, I. 2021). Interestingly, some manufacturers pursuing in-house production of growth factors have also already achieved significant cost reductions. This is consistent with other reports demonstrating cost-effective growth factor production at smaller laboratory scales (Kuo et al. 2020; Lyra-Leite et al. 2021).
The diversity of growth factors demanded may pose a challenge for suppliers.
Manufacturers across the industry are mainly using a similar set of key growth factors. However, the pursuit of species-specific and engineered versions is likely to increase the overall number that the industry will demand. Nevertheless, identifying key growth factors is critical for suppliers to meet the industry’s requirements and presents opportunities for pooled procurement at lower price points. Additionally, suppliers may have to make business plan adjustments based on expected or achievable profit margins for selling growth factors to the cultivated meat industry.
Pooled procurement opportunities
One area of alignment across manufacturers and suppliers was the desire for pooled procurement of media and growth factors. For instance, 92% of suppliers indicated they would be interested in offering reduced-price, volume-based arrangements for growth factors (n = 14). 82% of suppliers indicated they would be interested in supplying reduced-price, volume-based arrangements for cell culture media (n = 11). 100% of suppliers indicated that they would be interested in being contacted by manufacturers for co-manufacturing of growth factors (n = 15).
69% of manufacturers indicated they would also be interested in pooled procurement of growth factors, with another 25% answering that they were unsure (n = 16). The growth factors of greatest interest to manufacturers are listed below. Some manufacturers were interested in species-specific versions of these growth factors. Other growth factors than those listed here may be important for cultivated milk production.
- Insulin
- NRG1
- EGF
- TGFb1
- FGF
- IGF
- Transferrin
- LIF
- Albumin (based on inventory data from Vergeer, 2021)
Manufacturers and suppliers agree on the benefits of pooled procurement.
Aggregating demand for specific high-value and high-cost ingredients across many cultivated meat manufacturers can unlock lower prices and increase efficiency in the supply chain for growth factors. The survey data indicate that both manufacturers and suppliers are interested in pooled procurement arrangements, and candidate growth factors of interest have been identified. To our knowledge, current purchasing arrangements are made between individual manufacturers and suppliers. An entity that can procure growth factors on behalf of aggregated buyers could benefit the entire industry.
If you are interested in pooled procurement purchasing opportunities, please reach out to BlueCell Syndicates (andy@blueledgecap.com) to learn more.
References
- Kuo, Hui-Hsuan, Xiaozhi Gao, Jean-Marc DeKeyser, K. Ashley Fetterman, Emily A. Pinheiro, Carly J. Weddle, Hananeh Fonoudi, et al. 2020. “Negligible-Cost and Weekend-Free Chemically Defined Human iPSC Culture.” Stem Cell Reports 14 (2): 256–70.
- Lyra-Leite, Davi Marco, Hananeh Fonoudi, Mennat Gharib, and Paul W. Burridge. 2021. “An Updated Protocol for the Cost-Effective and Weekend-Free Culture of Human Induced Pluripotent Stem Cells.” STAR Protocols 2 (1): 100213.
- Sinke, P., Vergeer, R., Odegard, I. 2021. “LCA of Cultivated Meat: Future Projections for Different Scenarios.” CE Delft.
- Specht, Liz. 2018. “An Analysis of Culture Medium Costs and Production Volumes for Cell-Based Meat.” The Good Food Institute. https://www.gfi.org/files/sci-tech/clean-meat-production-volume-and-medium-cost.pdf.
- Vergeer, R., Sinke, P., Odegard, I. 2021. “TEA of Cultivated Meat: Future Projections for Different Scenarios.” CE Delft.
Authors and partners
The Good Food Institute partnered with Turtle Tree Scientific to conduct the industry survey and analysis.
Authors
Elliot Swartz, Ph.D.*
Lead Scientist, Cultivated Meat
The Good Food Institute *Corresponding author
Jess Nguyen
Business Manager
TurtleTree Scientific
Timothy Neo
MSAT Manager
TurtleTree Scientific
Fionna Lee
Chief People Officer
TurtleTree Scientific
Partners
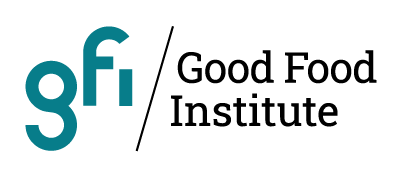
The Good Food Institute (GFI) is a 501(c)(3) nonprofit working internationally to make plant-based and cultivated meat delicious, affordable, and accessible. GFI advances open-access research, mobilizes resources and talent, and empowers partners across the food system to create a sustainable, secure, and just protein supply.

TurtleTree Scientific was founded out of a desire to solve the challenges of cellular agriculture. We’re producing food grade growth factors and cell culture media to design the necessary foundations for the industry to thrive. TurtleTree Scientific is started by TurtleTree and is led by an experienced team of industry professionals.
Related resources
Discover papers, GFI resources, ongoing research projects, and research opportunities related to cell culture media and growth factor trends in the cultivated meat industry.
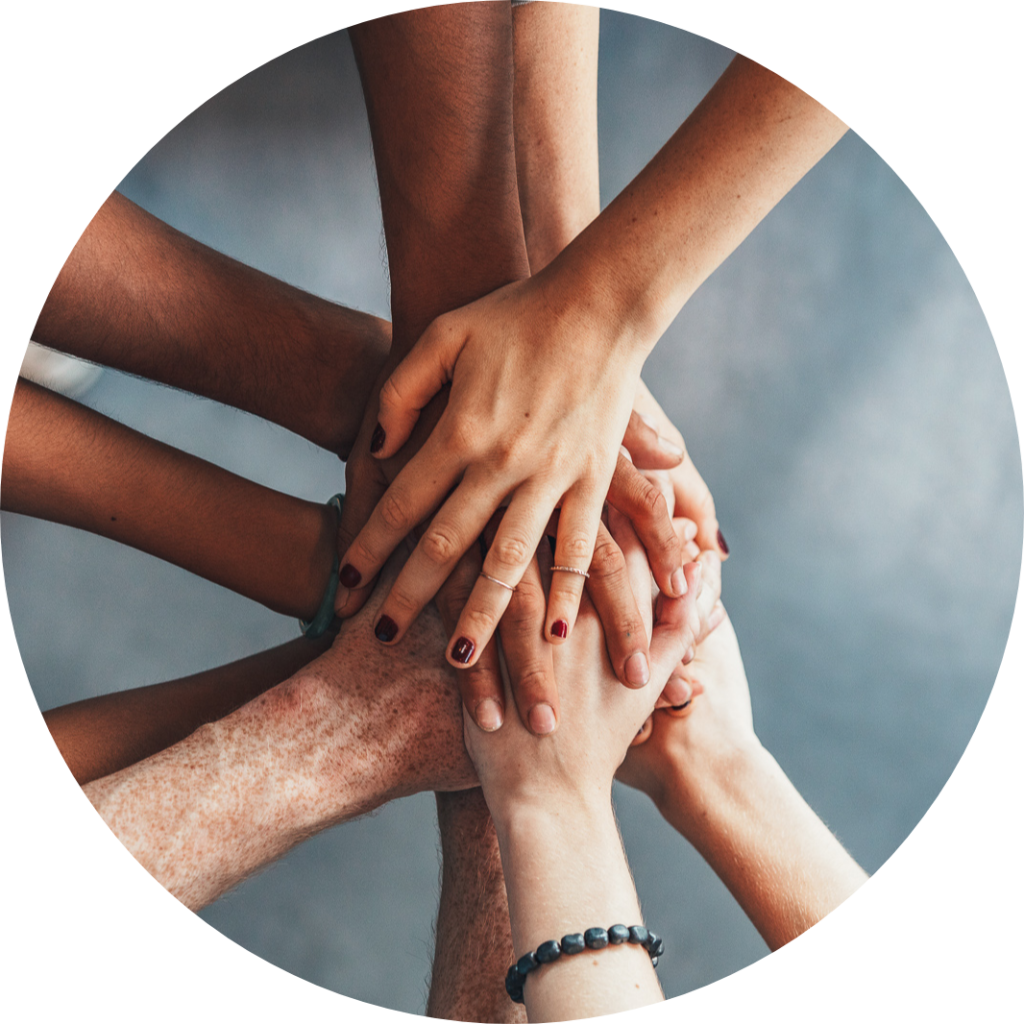
Support our work
Our industry engagement is made possible thanks to our generous, global family of donors. Philanthropic support is vital to our mission. Connect with us today to discuss how you can help fuel this transformative work.